ENGINEERING SINCE 1957
COMPONENTRY
FoamFabricators is a solutions-based company!
Unlike packaging where the molded foam part if typically protecting something else,here we’ll see examples where it’s part of or is the product. In most cases it’s replacing injection molded plastic and/or sheet metal.
Why? When replacing both substrates molded foam can:
- Manage vibration issues;
- Offer insulation (thermal) benefits;
- Keep tooling costs lower;
- Shorten lead times;
- Lower the cost and lead time for running changes;
- Gain form-fit possibilities by leveraging the resiliency of the foam.
CELEBRATING 60+ YEARS
OUR COMPONENTRY SERVICES
Material Selection, Engineering Design, Molded & Fabricated Solutions –All Delivered with over 65 Years of Experience with countless industries and applications. Some highlights:
Sports & Recreation
Because molded foam is dimensionally stable enough to be used as a component part, it floats, is inert and has terrific cushioning properties. It’s a great choice in the sports and recreation fields. From personal watercraft flotation and seating –molded foam is a wise and safe way to go.
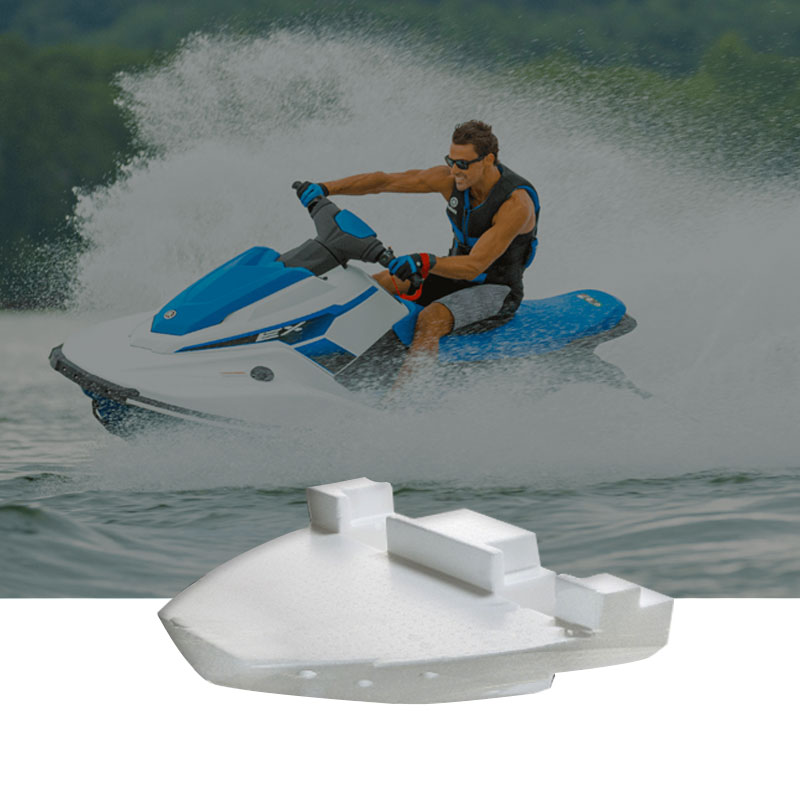
Display & Point-of-Purchase
Due to its strength and ability to generate almost any shape and texture, molded foam is a terrific material for point-of-purchase items and displays. For special applications, EPS can even be custom colored to meet your needs.
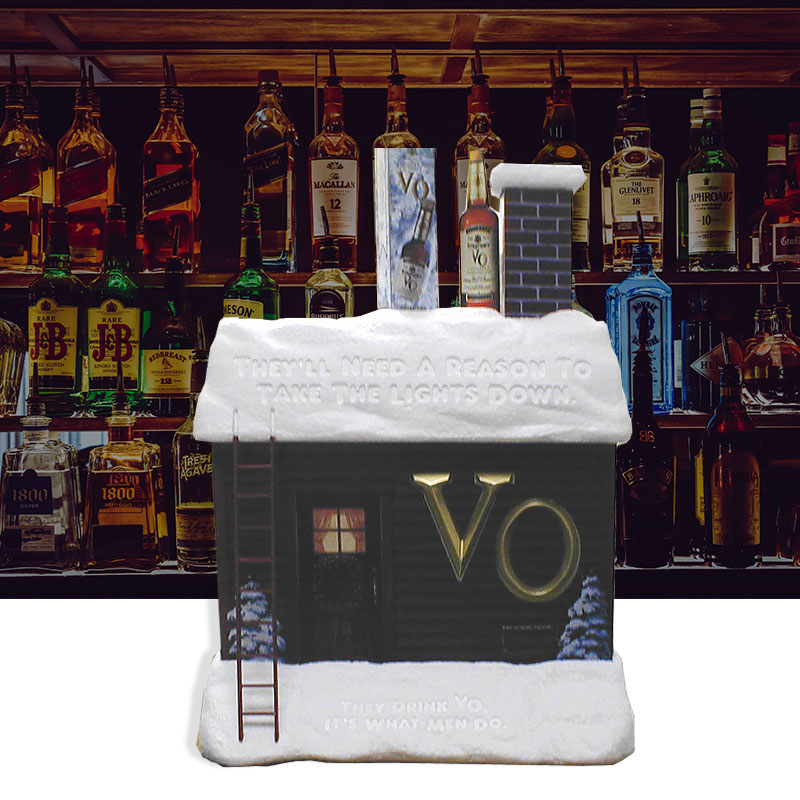
OEM Parts
Original Equipment Manufacturer (OEM) parts are “the part” not the packaging “on the part”. In this picture, you see a component that was over-molded and then installed as part of blood analyzing equipment.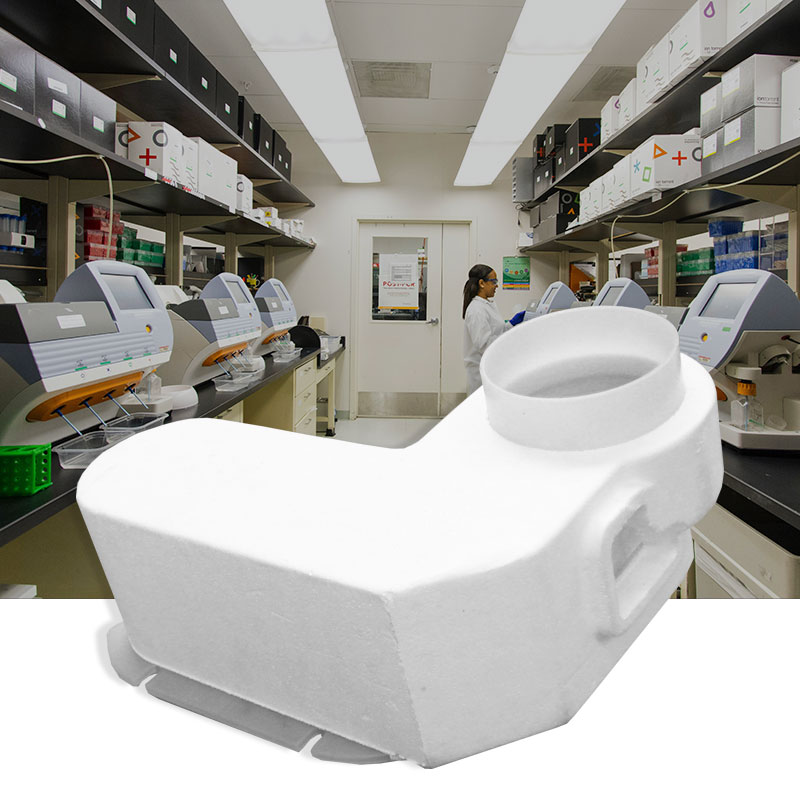
Construction Products
There are several areas in the construction market where molded foam is used.One of the fastest growing segments is insulated concrete forms or ICF’s. ICF’s are hollow sections of molded foam, usually made from EPS, that construction crews stack into the shape of the walls of the building. This procedure is a lot like assembling Lego blocks (the children’s toy). The center is then filled with concrete to create the structure. A typical four-inch-thick foam block wall is four to six times stronger than a conventional stick-built house, making it resistant to fire, violent winds and even earthquakes. The combination of high-mass concrete and the ICF’s provides permanent insulation for a quieter, more energy efficient home.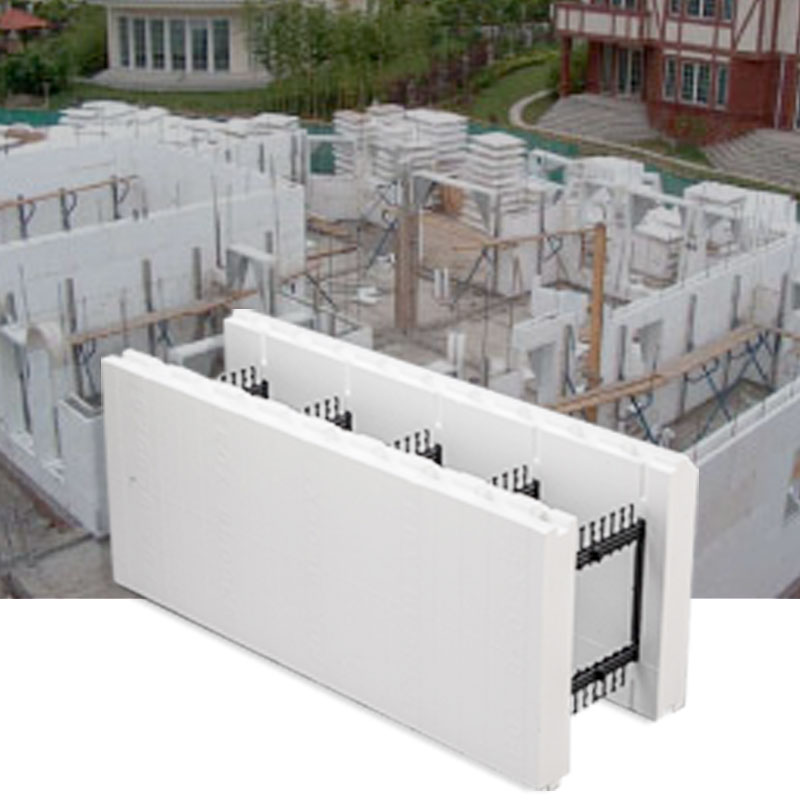
Automotive
Many types of molded foams are used in automotive applications due to the many benefits.
Lightweight. With product weight becoming a leading concern, lower density expanded plastic foams are and ideal choice for rigid chassis replacement. Parts made from expanded polypropylene (EPP) for example offer equivalent impact strength and toughness with 10 to 40 percent less weight than other classic chassis materials. It provides comparable impact strength with less excess weight.
Design Flexibility. Energy management doesn’t have to mean big and bulky. With its highimpact/density ratio, molded foam parts can be designed with thinner profiles and smaller shapes for excellence in impact protection and styling.
Economical. Expanded foam is easily reclaimed during the parts manufacturing operations.Scrap content can be five to ten percent with minimal changes in properties.
Recyclable. EPP parts are compatible with other olefinic component parts such as moldedpolypropylene (high tech, medical and automotive interior and exterior enclosures and panels) and thermoplastic olefin (TPO) fascias and cladding. More parts can be recycled without costly separation techniques.
Versatile. EPP can be molded as planks, shapes or profiles, and molded with a textured PP surface and resilient EPP foam core. With variable bead sizes, you can mold intricately shaped parts with smoother surfaces and thinner wall cross sections.
Resilient. Parts made with EPP have excellent resiliency to absorb multiple impacts without lossof cushioning properties.
Chemical and Heat Resistant. EPP-based parts resist many common solvents and chemicals suchas oils, gasoline and diesel fuels, and antifreezes. EPP-based parts withstand high temperaturesup to 212F (100C) without warpage or changes in dimension
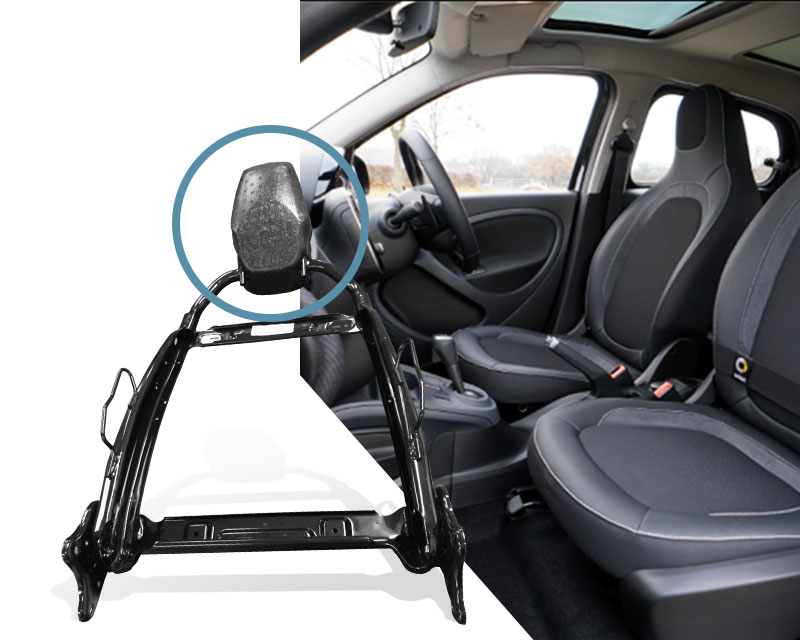
Recreational Vehicles (RVs)
Expanded polystyrene (EPS) has been an excellent choice for an RV wall substrate for years. Normally used as a foam core laminated between an inside and outside skin (usually aluminum) it creates an envelope around the whole RV.
A molded roof panel for high volume requirements is a good example of how the initial investment in a tool can be offset by the increased savings when compared to cutting and fabricating these same EPS panels. The production cost per unit for molded panels is usually much less than traditionally manufactured roof sheets and/or fabricated parts. Another advantage is the predictable, reliable quality of the molded part when it comes to dimensional tolerances and physical properties.
By also taking a closer look at the OEM and Automotive sections you’ll begin to see how molded foam is much more than a packaging material. In fact,there are many applications in an RV where molded foam is replacing wood, metal and hard plastics already.
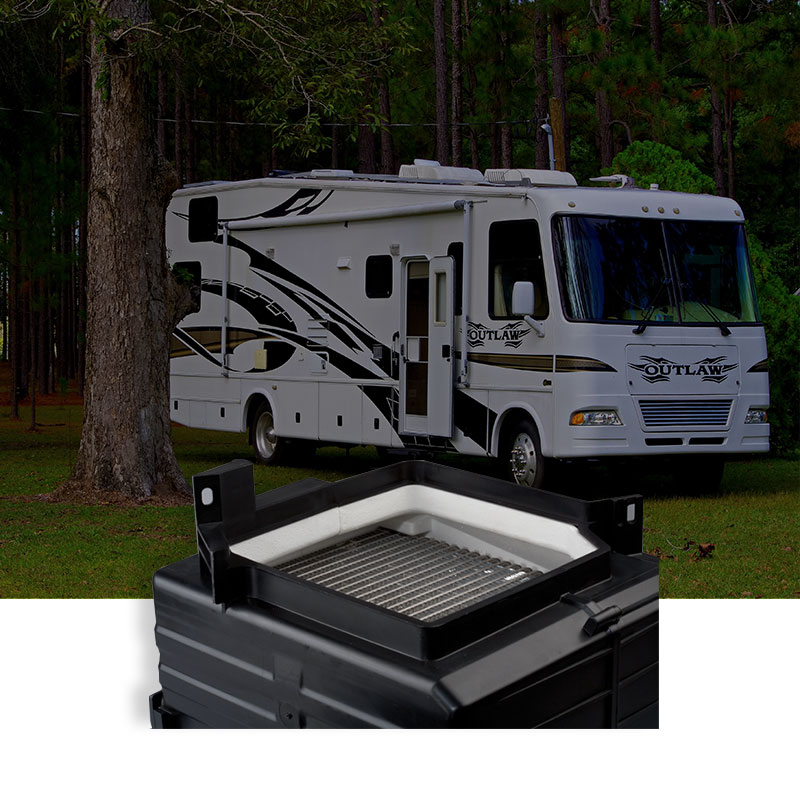

We look forward from hearing from you. Whether is is a stock item you need quickly or a custom project fulfilled, Altor Soliutions is your solution for everything PIC.
Contact Us
Phone Number
508 234-6323
888 740-3626